Concrete Slab Prep Tips for Rio Rancho Build
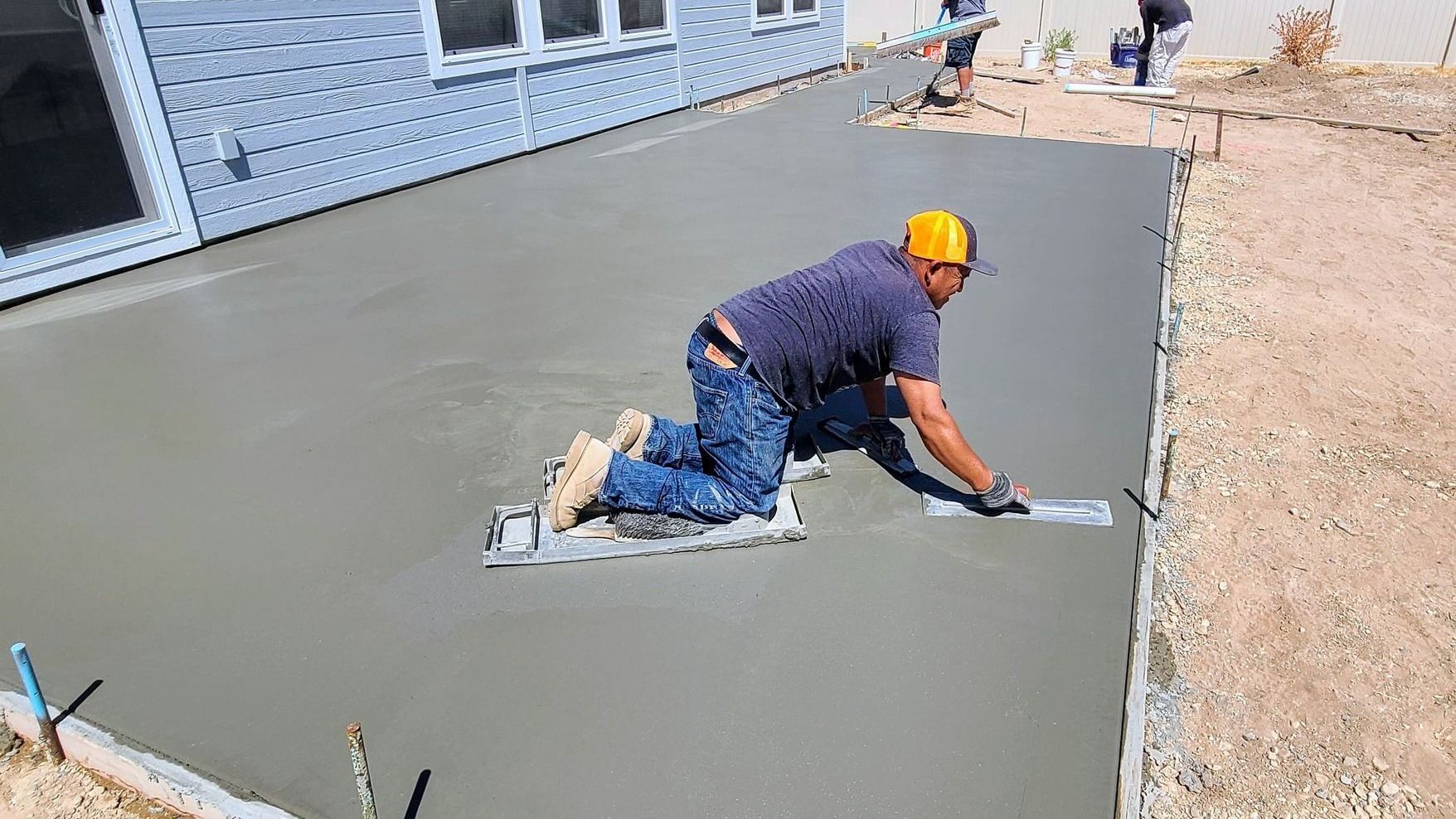
A solid slab starts long before the concrete is poured. In Rio Rancho, where the soil and climate create unique construction challenges, proper slab preparation is essential for long-term strength, durability, and performance.
Whether you’re building a home foundation, patio, driveway, or commercial floor, the prep work underneath determines how well that concrete holds up. Cutting corners at this stage can lead to cracks, sinking, drainage problems, and costly repairs.
Here are key slab preparation tips every builder and homeowner should follow to ensure a stable, long-lasting result.
Evaluate Soil Conditions First
The first step is understanding the soil. Rio Rancho has areas with expansive clay and sandy soil, both of which can cause movement over time. Conduct a geotechnical soil test to determine compaction, moisture content, and how the soil behaves under load.
If soil conditions are poor, excavation and replacement with engineered fill may be necessary. Stabilizing the subgrade helps prevent future shifting and settlement.
Compact the Subgrade
Once soil is addressed, the subgrade needs to be compacted. Loose or poorly compacted subgrades allow the slab to move and settle unevenly. We use plate compactors and vibratory rollers to reach the recommended density.
For most residential builds, the subgrade should be compacted to at least 95 percent of its maximum dry density. This ensures the ground won’t shift under the weight of the concrete.
Add a Stable Base Layer
A strong base prevents slab cracks and water-related damage. Most projects benefit from a 4–6 inch layer of compacted gravel or crushed rock beneath the concrete. This base acts as a drainage layer and helps distribute weight evenly.
Avoid using soft sand as a base—it can shift when wet. A well-graded gravel mix performs best.
Set Forms and Ensure Proper Grading
Formwork holds the shape of the slab. Forms must be level and securely staked, with proper slope to direct water runoff. For outdoor slabs, a slope of at least 1/8 inch per foot away from structures is recommended.
Getting the grading right protects your slab from water pooling, erosion, and freeze-thaw damage.
Use Vapor Barriers for Interior Slabs
For indoor slabs or garages, a vapor barrier between the base and the concrete helps prevent moisture from rising through the slab. This is especially important for slabs receiving flooring like wood, tile, or epoxy.
The barrier should be a minimum 10-mil polyethylene sheet, sealed at joints and edges to provide continuous coverage.
Install Reinforcement the Right Way
Reinforcement prevents cracks and adds tensile strength. Use welded wire mesh or rebar depending on the slab’s thickness and load requirements. Rebar should be supported on chairs so it sits in the middle of the slab—not on the ground.
This helps the concrete absorb stress from traffic, weight, and soil movement.
Plan for Expansion and Contraction
Concrete expands and contracts with temperature changes. Control joints and expansion joints prevent random cracking. These joints should be planned during the layout and cut within 24 hours of pouring.
Spacing depends on slab thickness but generally should not exceed 10–12 feet in any direction.
Don’t Skip Moisture Control
Drainage matters. Slabs must be prepped to shed water properly—both on the surface and from below. Poor drainage increases the risk of erosion, slab heave, and freeze-thaw damage.
We recommend perimeter drains, sloped grades, and downspout extensions for all exterior slabs.
Timing and Weather Considerations
Avoid pouring concrete during extreme weather. Too hot, and it sets too fast. Too cold, and it won’t cure properly. Prep should include contingency plans for weather changes, such as curing blankets, additives, or sun shades.
In Rio Rancho’s climate, early morning pours during mild weather work best.
Final Prep Checklist Before the Pour
- Soil tested and stabilized (if needed)
- Subgrade compacted to 95% density
- Gravel base installed and compacted
- Forms level and secure with proper slope
- Vapor barrier installed (for interior slabs)
- Reinforcement placed and supported
- Control joints planned
- Drainage measures confirmed
- Weather forecast checked
Conclusion: Prep Like a Pro
Strong concrete begins below the surface. If you want a slab that holds its shape, resists cracking, and lasts for years, prep is everything.
At Elite Form Concrete, we take slab preparation seriously. From soil stabilization to steel placement, we make sure every base is covered—literally. Reach out today to get your concrete project off to a strong start.